STL6 - SLANT LATHE TURNING CENTER with TAILSTOCK -
STL6 - SLANT LATHE TURNING CENTER with TAILSTOCK - is backordered and will ship as soon as it is back in stock.
Couldn't load pickup availability
Delivery and Shipping
Delivery and Shipping
Add some general information about your delivery and shipping policies.
Video Links
Smithy Training Videos - Learning to Machine on a Lathe Mill Combo
Years ago, Smithy produced a series of videos about learning to machine on a lathe mill combo machine. We hear often that these videos have been very helpful. This series is used in quite a few schools and tech training centers, literally throughout the world. Teachers like these videos because the concepts of machining are presented in a very logical way. Hopefully these videos will be helpful to you.
Best Practices - Lathe Turning
Introduction to standard metal late operations. An introduction to basic metal turning concepts is provided, along with basic instructions on lathe operation.
Workholding & Set up
Review of guidelines for installing a variety of work piece types and sizes on a metal lathe. This video covers turning between centers and proper mounting of a work piece in a lathe chuck. Proper use of lathe follow rests and steady rests is included.
Cutting Tool Selection
This video explains the selection and use of single point cutting tools on the lathe. Choosing the right cutting tool for a given operation is an important step when setting up a lathe. Selecting tool types and cutting speeds is also reviewed.
Facing Operations
This video demonstrates proper procedures and operator work process management for lathe turning and facing operations on a metal turning lathe. Reviews the various lathe turning operations that are typically used in a small shop setting.
Bench Top Milling & Drilling
Reviews the concepts of milling and drilling on a metal cutting mill/drill machine. Common practices in milling and drilling operations are presented. Tutorial on selecting best milling and drilling operations for a given task are provided.
Cutting Tool Selection
This video explains the selection and use of end mills and drill bits is covered. Choosing the right cutting tool for a given operation is an important step when setting up for a milling or drilling project. The foundation concept of selecting the best rotating cutting tool and cutting speed for a given project is also reviewed.
Workholding & Set-up
There are a wide variety of workholding tools that can be used to hold a work piece for milling or drilling operations. This video reviews the different concepts and practices in workholding for mill/drill operations. This video also offers some suggestions on workholding accessories to help you get started.
Basic Milling & Drilling Operations
This video starts by showing you machine controls used for milling and drilling operations on a small mill/drill machine. In this case, the Smithy Granite. The video also covers basic concepts and practices for effective metal milling and drilling on a bench top mill/drill machine.
Proper Machine Tool Maintenance
Proper maintenance of every machine tool is the key factor in that machine's ability to machine accurately and efficiently. Lubrication and maintenance are a big factor in assuring long life for every bench top lathe or mill/drill machine.
User Stories
Testimonials from Smithy's happiest customers
No Wait Time With My Smithy
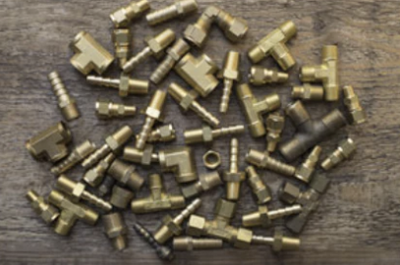
"I have a granite 1324. I run a job shop outfit that does machining work for plastics manufacturing companies. My customers sometimes have orders with 2 or 3 day turn-around. I work in aluminum, plastic, and brass. What I enjoy most about Granite is the lathe work. It is really easy."
-Hai David Nguyen, L.K.B TX
More Convenient for Hobbyists
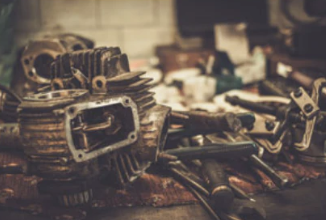
"I use my Smithy to make or modify parts for motorcycles and antique guns. I'm in this as a hobby. The Smithy probably has paid for itself but I haven't kept track. What is more important to me is the convenience of making my own parts, exactly as I need them when I need them."
-Kerry Klein, MI
Support Leads the Way

"I looked at other machining equipment but chose Smithy because of the quality, size, and availability of tech support. It's compact yet it does the work of larger units. It's a lot of machine that takes up a little space and it will pay for itself in the long run."
-Danny A. KY
Better Than a Grizzly
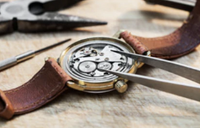
"After technical school, I did an apprenticeship in clock and watch repair and in tool and die making. I'm retired now and run a busy clock repair shop with my Smithy. I make parts for older clocks, cut clock gears, and make the cutters as well overhaul clock repair tools. I purchased a 9" x 19 bench lathe from Grizzly but returned it because of poor quality. I chose Smithy for its Sturdiness, its milling capabilities, and its compact size."
-William V-R., GA
No more down time
"Wendell and his business partner own a small textile factory. Last year, a German sewing machine clutch broke and production stopped. They weren't sure how long it would take to get a replacement part or if they could even find one. Putting their Smithy to work instead, they had the sewing machine back in production the same day."
-Wendell(Owner of Small Textile Company)
PRODUCT INFO
5/7.5 HP Servo Spindle
OVERVIEW
Slant Bed CNC Turret-Tailstock Lathe
The high quality, 8-position turret has high positioning accuracy and repeatability. Bi-directional indexing of the turret allows for the shortest indexing and cycle time.
- Siemens 808D CNC Control
- Servos and Closed Loop System
- True Slant Bed – Mono-Block Casting
- Servo Spindle – High Speed/Torque
- 2” Spindle Bore
- 7.5 HP Spindle
- Travel: X = 6”/Z = 12”
- 800 IPM Feed Rate
- 50-3000 RPM Spindle
- Schneider Electrical Components
- Bi-directional Indexing Turret
- Hydraulic 6" 3-Jaw Chuck
- Hydraulic Tail Stock
- 18 months on STL6 lathe
- 3 years total (2+1)on Siemens 808D Control
FEATURES
Lathe Machine | |
Mono-Block Cast Iron - True Slant Bed | One piece cast iron foundation is a true 35 degree slant bed casting, providing large mass in a small footprint. More mass means higher rigidity and better heat dissipation. |
Slant Bed Design | A slant bed lathe allows for better chip flow. A slant bed lathe can handle a large volume of chips, while protecting the ways from chips and debris. The operator has easier access to the chuck and work table with a slant bed - easier for set-up. |
Full Enclosure | Machine is completely enclosed with a sliding front access door and easy access panels on tailstock end and machine back side. Coolant and chips are enclosed and properly recycled. Electromagnetic lock keeps operator safe. |
1.89” Spindle Bore | With A2-5 spindle nose. Generous bore size for easy pass through of large stock and easy access for optional pneumatic or hydraulic chuck. Adaptable for automatic bar feeder. |
Hydraulic 6” 3-Jaw Chuck | Standard features include a 6" hollow bore hydraulic actuated 3-Jaw Chuck. |
8-Tool Precision Bi-Directional Turret | Electric indexing turret allows for flexibility in tooling and programming option. Turret lathes tend to be easier to program, especially when cutting complex parts. Bi-direction changes allows for higher speed and efficiency. |
Hydraulic Tail Stock | Hydraulic actuated tail stock slides on it's own set of linear ways that are positioned in front of and parallel to the machine bed ways. The tailstock body is positioned by a tracton bar, and automatically driven by a hydraulic actuator. Up to 90% more efficient when compared to a manual tail stock. |
Tool Box and Tools | A set of the basic tools required for maintenance are included with this lathe. Gives you what you need to get up and running and for routine maintenance. |
Foundation Pads | Heavy machined leveling pads adjust the height to keep your machine aligned and balanced. Solid multi-point contact with shop floor reduces vibration, and increases accuracy. |
Drive System | |
7.5 HP Servo Spindle Drive | Plenty of power to match the machine’s capacity - nearly twice the power of comparably priced machines. Capable of rigid tapping and spindle positioning. |
50-3000 Spindle Speed Range | Infinitely variable speed changes, from 50 to 3000 RPMs in a single speed range. No need for changing gears or belts. |
Schneider Electrical Components | One reason we can offer an 18 month machine warranty is because of the recognized quality and reliability of Schneider Electrical components. Highest reliability rating - highly efficient design reduces power usage. |
PMI Ball Screws | World-class standard ball screws - efficiently transmit rotary motion to linear motion, allowing for high-speed, highly accurate axis movements. Accurate ball circle diameters through length of ball screw assures consistent drag torque and low noise. |
Precision Hiwin Linear Guideways w/Telescoping Covers | World-class standard linear motion guideways come standard on the TS-1117. Stainless steel telescoping guards provide maximum protection of guideways from chips and coolant. |
Feed Rates: 800 IPM on X / 1000 IPM on Y | Good power, plus high-quality linear guides and ball screws turn this lathe into a high speed turning center. The Siemens industrial CNC control and axis servo drive system provide the power and control that allows for higher speeds. cutting and rapid feed rates are many times faster than competitive systems. |
Safety/Operation | |
Ergonomic Control Panel and Operator Interface | Machine control panel adjusts and rotates up to 90 degrees. High tactile buttons, manual pulse generator, and convenient cycle start buttons improve operator convenience, efficiency, and safety. |
Auxiliary Cycle Start | Easy access buttons allow operator to operate pneumatic or hydraulic chuck with the push of a button. Having a second E-Stop within easy reach also adds to the safety features of this lathe. |
Manual Pulse Generator | Handheld pendant that allows the operator to be independent from the main control panel. The rotating knob generates pulses that are sent to the machine control, allowing the operator to move the lathe in a predetermined distance with each click of the knob. |
Automatic Lubrication System | Lubricates all wear points during machine operation at continuous time intervals. Benefits include reduced labor and material costs and significant extension of bearing life. |
Programmable Coolant System | Control coolant flow at the control panel, using standard M-Codes. Cycle times can be significantly reduced, while feed and cutting speeds may be significantly increased. Proper cooling extends life of cutting tools. |
Work Light | Focused lighting elements increase operator efficiency and reduce fatigue. This light is flicker resistant, waterproof, and resistant to both cooling and lubricants. It is also resistant to impacts and vibrations. |
Tri-Color Alarm Light | Green light turns red when control alarm recognizes a machining error or machine malfunction. An operator standing away from the machine is visually alerted by the activated alarm light when machining cycle is finished or machine errors out. |
Siemens 808D CNC Control | |
Closed Loop System | System directly monitors motor position and velocity in real time. The system then automatically makes corrections to assure the correct tool positioning. High accuracy and maximum parts quality ensure a minimal rejection rate. Also assures smoother surface finishes. |
Siemens Servos and Drives | Achieves rapid acceleration and higher speeds - maintains high torque throughout speed range. Motor is highly efficient - and it stays cool. Quiet at high speeds while remaining vibration free during operation. |
Ideal for CNC Beginners | Ideal for entry level CNC users, the innovative, integrative startGUIDE from Siemens provides an on-line digital help function on every screen. Helpful instructions are available anytime - at a push of a button. |
Simple & Intuitive Interface | Well designed conversational programming functions and Wizards from Siemens help streamline programming at the control panel. All Siemens 808D controls come standard with this SINUMERIK Operate BASIC functionality. |
Compact and Robust | Industrial panel design with hardened features is ideal for harsh environments. Small compact design matches smaller machines tools like the AutoMateCNC line. |
USB Connector Easily Handles Large Files | This unique Siemens function allows for the streaming of large program files direct from a USB. Large files are no longer a concern - other CNC systems lack this robust level of functionality. |
Built-In Helps | Several Siemens provided “assists” help streamline programming functions. One example would be Hot Keys. With the Hot Key function, machine operators can easily access commonly used screens using operator defined hot keys. |
SPECIFICATIONS
GENERAL SPECIFICATIONS - AUTOMATE CNC TURNING CENTERS | ||||
Photo |
![]() |
![]() |
![]() |
![]() |
Model Name | FL300-II Flat Bed Turning Center | FTL320 Flat Bed w/ Tailstock | SL6 Slant Bed Turning Center | STL6 Slant Bed Turning Center w/ Tailstock |
Price | $23,459 | $24,699 | $25,995 | $31,989 |
TURNING CAPACITIES | ||||
Max Swing Over Bed | 17.5” | 18" | 15.75" | 17” |
Max Swing Over Carriage | 5.25” | 6.5" | 7.85" | 8.5” |
Max Length of Workpiece | 7” | 20" | 11.8" | 9” |
Machine Repeatability | .0002” | .0002" | .0002" | .0002” |
TRAVELS & FEED RATES | ||||
X Axis | 14” | 7.5" | 11.75" | 6” |
Z Axis | 12” | 13.5" | 14" | 11.75” |
X-Axis Rapids | 950 IPM | 984 IPM | 800 IPM | 750 IPM |
Z-Axis Rapids | 950 IPM | 400 IPM | 800 IPM | 800 IPM |
Max Cutting Speed | 315 IPM | 315 IPM | 315 IPM | 315 IPM |
SPINDLE | ||||
Spindle Power | 4 HP | 7.37 HP | 7.5 HP | 5 HP (7 HP Optional) |
RPM Range | 50-3000 | 50-3000 | 50-3000 | 50-3000 (5000 Optional) |
Spindle Bore | 1.46” | 1.89" | 1.89" | 1.89” |
Spindle Nose Taper | A2-4 | A2-5 | A2-5 | A2-5 |
Chuck Type | Pneumatic Chuck | 6" Manual 3-Jaw Chuck | 6" Manual 3-Jaw Chuck | 6” Manual 3-Jaw Chuck (Hydraulic Chuck Optional) |
WEIGHT/DIMENSIONS/CAPACITIES | ||||
Machine Weight | 4220 Lbs | 4720 Lbs | 4800 Lbs | 5500 Lbs |
Machine Dimensions | 80” x 58” x 67.5” | 82" x 60" x 68" | 86.5" x 63" x 72" | 87” x 64” x 72” |
Shipping Weight | 4600 Lbs | 5378 Lbs | 5492 Lbs | 5960 Lbs |
Air for Pneumatics | 90 PSI | N/A | 90 PSI | 90 PSI |
Coolant Capacity | 11 Gal | 11 Gal | 25 Gal | 21 Gal |
Hydraulic Capacity | 11 Gal | N/A | 18.5 Gal | 18.5 Gal |
Power (Standard) | 220V 3 Phase Power | 220V 3 Phase Power | 220V 3 Phase Power | 220V 3 Phase Power |
Amperage Requirements | 20 Amp | 30 Amp | 35 Amp | 29 Amp |
-
MI-409 PRO - Features
1) Gear Drive X Axis Power Feed: Adjust the hand located on the left side of the machine base to engage, disengage and change direction on the X axis power feed gear drive.
2) Gear Drive Y Axis Power Feed: Adjust the handle located on the right side of the machine base to engage, disengage and change direction on the Y axis gear drive.
3) Powered Mill Head Lift: Raise and lower mill head with the push of a button. No more hand cranking required.
4) Gear Drive Mill Quill with Auto-Feed: Smooth milling feed with auto adjustment for depth of cut. Provides rapid, accurate milling, as well as capabilities for tapping and boring. Allows for tapping of blind holes and boring to chosen depth.
Financing Options
Consumer / Personal Financing
- 48-month financing plan
- 5.99% interest rate
- Promotional Financing Plan only when purchasing Smithy equipment
Commercial / Business Financing
- Soft-pull credit - doesn't affect credit score
- Flexible rates and payment plans
- Approval with low credut
Canada - Business Financing
- Soft-pull on credit - doesn't affect credit score
- Flexible rates and payment plans
- Approval with low credit
WHO BUYS THESE MILLS FROM SMITHY?
Businesses/Professional: Schools purchase quite a few. As so military organizations, R & D labs, etc. Small machine shop/production shops are frequent buyers.Garage/Home Shops: The machines are designed and built for professional parts production settings. Because of the quality features - and reasonable price - these rugged milling machines are also popular with home and garage shop machinists.
IS THE TOOL PACK HELPFUL?
The FREE tool pack is intended to proved a basic tool set-up to get you started when your machine arrives. It’s a balanced set of tooling, but you will likely need more tooling once you figure out specific projects you want to do.
WHAT DO YOU MEAN BY “INSPECTED TWICE?”
Each lathe is inspected by trained company employees at the factory - PLUS, a second complete inspection is performed at our warehouse in Ann Arbor, MI before it is sent to the customer.
WHY ARE THESE MILLS BETTER THAN OTHERS ON THE MARKET?
For a machine tool to be truly great it must have attention paid to every step of its development - design, production, quality control, testing, and after sales support. No other bench top lathe on the market, at this price, has the same level of quality commitment at every step as these MIDAS mills.
HOW LONG HAVE YOU BEEN SELLING THESE MILLS?
Over 30 years.
DO MANY LATHE BUYERS ALSO PURCHASE MILLING MACHINES?
Yes, the MI-1440 lathe matches well with the MI-409MZ milling machine - a machine shop combo that was built to last. Many customers buy this combination.
WHY SHOULD I BUY A MILLING MACHINE FROM SMITHY?
Rugged Design
Quality Built In
Inspected Twice
Best Service Support
The best bench top mill value - for over 30 years!
DO I NEED TO BE A MACHINIST TO USE THE MACHINE?
NO, many buyers of these machines don’t have the experience. What they have is the need to make a certain part or product. What you need is a commitment and curiosity. We have a set of machining training videos on our website. You can usually find classes at a local community college or vo-tech school. Get a machine and get going! You won’t be disappointed.
Payment & Security
Payment methods
Your payment information is processed securely. We do not store credit card details nor have access to your credit card information.
Overview
Use this section to highlight specific product features to your customers.
Product comparison grid
Add content here to explain a bit about the range of products on offer and which ones may be most suitable for your customers.